-
- News
- Books
Featured Books
- design007 Magazine
Latest Issues
Current IssueLevel Up Your Design Skills
This month, our contributors discuss the PCB design classes available at IPC APEX EXPO 2024. As they explain, these courses cover everything from the basics of design through avoiding over-constraining high-speed boards, and so much more!
Opportunities and Challenges
In this issue, our expert contributors discuss the many opportunities and challenges in the PCB design community, and what can be done to grow the numbers of PCB designers—and design instructors.
Embedded Design Techniques
Our expert contributors provide the knowledge this month that designers need to be aware of to make intelligent, educated decisions about embedded design. Many design and manufacturing hurdles can trip up designers who are new to this technology.
- Articles
- Columns
Search Console
- Links
- Events
||| MENU - design007 Magazine
In Deep: The Art and Science of DFM with Gary Ferrari
February 8, 2017 | Andy Shaughnessy, PCBDesign007Estimated reading time: 2 minutes
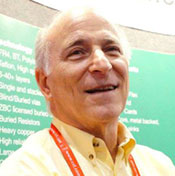
When the topic of DFM techniques came up, I knew I had to talk with Gary Ferrari of FTG Corp. Gary has been involved with designing and manufacturing PCBs for decades, and he’s the past co-founder and executive director of the IPC Designers Council. I caught up with Gary between Thanksgiving and Christmas, and we conducted the following interview.
Andy Shaughnessy: Give us a quick background on yourself and your role at FTG.
Gary Ferrari: I have been in this industry for more than 50 years. The major portion of this time has been spent in PCB design and manufacturing. I have spent some time in assembly, industrial robotics, and nuclear and fossil power plant controls systems design.
I serve as the Director – Technical Support for FTG Circuits. My main function has many facets. First is to work with our customer base during the design phase of their products. I help them design for manufacture, which includes fabrication, assembly, repair, reliability, and field service. This includes end-product performance, both electrically and mechanically. It sounds like a lot, and it is. To meet today’s advanced products within short design cycles, one must consider all these areas when selecting materials, components, etc.
Second is to represent them within the standards develop committees of IPC. Many current-day issues are discussed during the development meetings, which affect both our company and our industry. There are so many new, advanced technologies cropping up constantly. One must stay on top of them if one expects to survive in this industry.
I also provide IPC designer certification through EPTAC, an IPC licensed training center. These courses are quite extensive, exposing the attendees to many of the issues affecting successful designs.
Shaughnessy: So, what can PCB designers do to make the fabrication process go smoother?
Ferrari: The most important item that a designer can do is to talk to their fabrication and assembly suppliers. Ask them about how your design practices are affecting their ability to manufacture with low yields and high reliability. Most important is to find out the areas that are the most troublesome. The designer has many ways to attack a given issue, and may be able to select a design solution that is easier to manufacture, resulting in higher reliability and lower cost. This is most important when doing a new design utilizing a technology that is new to the company. Most fabricators can draw from experiences gained through a wide variety of technologies they have worked with through a large customer base.
To read this entire article, which appeared in the January 2017 issue of The PCB Design Magazine, click here.
Suggested Items
Cadence, TSMC Collaborate on Wide-Ranging Innovations to Transform System and Semiconductor Design
04/25/2024 | Cadence Design SystemsCadence Design Systems, Inc. and TSMC have extended their longstanding collaboration by announcing a broad range of innovative technology advancements to accelerate design, including developments ranging from 3D-IC and advanced process nodes to design IP and photonics.
Ansys, TSMC Enable a Multiphysics Platform for Optics and Photonics, Addressing Needs of AI, HPC Silicon Systems
04/25/2024 | PRNewswireAnsys announced a collaboration with TSMC on multiphysics software for TSMC's Compact Universal Photonic Engines (COUPE). COUPE is a cutting-edge Silicon Photonics (SiPh) integration system and Co-Packaged Optics platform that mitigates coupling loss while significantly accelerating chip-to-chip and machine-to-machine communication.
Siemens’ Breakthrough Veloce CS Transforms Emulation and Prototyping with Three Novel Products
04/24/2024 | Siemens Digital Industries SoftwareSiemens Digital Industries Software launched the Veloce™ CS hardware-assisted verification and validation system. In a first for the EDA (Electronic Design Automation) industry, Veloce CS incorporates hardware emulation, enterprise prototyping and software prototyping and is built on two highly advanced integrated circuits (ICs) – Siemens’ new, purpose-built Crystal accelerator chip for emulation and the AMD Versal™ Premium VP1902 FPGA adaptive SoC (System-on-a-chip) for enterprise and software prototyping.
Listen Up! The Intricacies of PCB Drilling Detailed in New Podcast Episode
04/25/2024 | I-Connect007In episode 5 of the podcast series, On the Line With: Designing for Reality, Nolan Johnson and Matt Stevenson continue down the manufacturing process, this time focusing on the post-lamination drilling process for PCBs. Matt and Nolan delve into the intricacies of the PCB drilling process, highlighting the importance of hole quality, drill parameters, and design optimization to ensure smooth manufacturing. The conversation covers topics such as drill bit sizes, aspect ratios, vias, challenges in drilling, and ways to enhance efficiency in the drilling department.
Elevating PCB Design Engineering With IPC Programs
04/24/2024 | Cory Blaylock, IPCIn a monumental stride for the electronics manufacturing industry, IPC has successfully championed the recognition of the PCB Design Engineer as an official occupation by the U.S. Department of Labor (DOL). This pivotal achievement not only underscores the critical role of PCB design engineers within the technology landscape, but also marks the beginning of a transformative journey toward nurturing a robust, skilled workforce ready to propel our industry into the future.