-
- News
- Books
Featured Books
- design007 Magazine
Latest Issues
Current IssueLevel Up Your Design Skills
This month, our contributors discuss the PCB design classes available at IPC APEX EXPO 2024. As they explain, these courses cover everything from the basics of design through avoiding over-constraining high-speed boards, and so much more!
Opportunities and Challenges
In this issue, our expert contributors discuss the many opportunities and challenges in the PCB design community, and what can be done to grow the numbers of PCB designers—and design instructors.
Embedded Design Techniques
Our expert contributors provide the knowledge this month that designers need to be aware of to make intelligent, educated decisions about embedded design. Many design and manufacturing hurdles can trip up designers who are new to this technology.
- Articles
- Columns
Search Console
- Links
- Events
||| MENU - design007 Magazine
Estimated reading time: 2 minutes
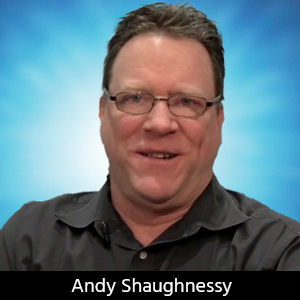
The Shaughnessy Report: Mistakes Were Made
Let’s just state for the record that no one wants to make a mistake.
I think it’s just a matter of human nature. It starts in elementary school; nobody wants to stand in front of the class at the blackboard and get a math problem wrong. If you do, it’s a long walk back to your desk!
Yes, we humans hate to face the looks of opprobrium from our fellow man. So, we go out of our way to avoid making mistakes.
The PCB industry is no different. Fortunately, PCB designers, design engineers, fabricators, and assembly providers generally do what it takes to create a PCB that functions in the field as desired. But mistakes do happen.
What does your company do when a board fails? When the board is designed, fabricated and assembled by three different entities, not to mention shipped by a fourth, figuring out what went wrong can be difficult, not to mention time-consuming.
Naturally, we’re approaching this equation from the point of view of the PCB designers and design engineers, because they tend to bear the brunt of the blame when a PCB starts smoking. And design is at the front end, so PCB fabricators and assemblers have no problem casting a suspicious eye upstream.
I’m sure you designers have heard it all from the fab and assembly folks: “How did you all screw up that design so badly? We built it the way you wanted it. Don’t your software tools do most of the real work for you? Turn off the Pink Floyd and get cracking!”
We started planning this issue with a survey sarcastically titled, “Whose fault is that bad board?” We asked a variety of questions regarding how the cause or causes of failure were determined, and what companies do to keep from making the same mistake again.
We asked the question “If a board fails in the field, whose fault is it, typically?” Here are some of the answers, slightly edited for clarity:
- Equipment set-up not followed, test procedure not followed, and demo manual not adhered to.
- The component manufacturer’s.
- We put our boards through a lot of testing before they get to the field. It is usually an unforeseen stress or other phenomenon that instigates the failure.
- This is twofold: The last person to handle the assembly and the final failure analysis outcome results.
- As far as the designer's responsibility, in most cases difficult technologies are discovered before the order is accepted, if not shortly thereafter. This affords an opportunity to improve upon the original design in concert with the designer, resulting in a potential savings in time to manufacture and cost to the customer.
- It could be anyone's fault. It can be the designer plus the fabricator, the fabricator plus assembly, or it could even be everyone’s fault.
- The designer. By designer, I mean the board architect (the guy who chooses the devices), the design engineer who does the schematics, a lack of SI/PI engineer, and the CAD engineer (who is doing a high-speed board without adequate and relevant knowledge).
To read this entire column, which appeared in the August 2017 issue of The PCB Design Magazine, click here.
More Columns from The Shaughnessy Report
The Shaughnessy Report: Design Takes Center Stage at IPC APEX EXPOThe Shaughnessy Report: The Myriad Opportunities—and Challenges
The Shaughnessy Report: In Bed With Embedded
The Shaughnessy Report: Pulling Together
The Shaughnessy Report: The Winds of Change
The Shaughnessy Report: Trace Oddity
The Shaughnessy Report: Simply Speaking
The Shaughnessy Report: Exploring High-reliability Fabrication