-
- News
- Books
Featured Books
- design007 Magazine
Latest Issues
Current IssueLevel Up Your Design Skills
This month, our contributors discuss the PCB design classes available at IPC APEX EXPO 2024. As they explain, these courses cover everything from the basics of design through avoiding over-constraining high-speed boards, and so much more!
Opportunities and Challenges
In this issue, our expert contributors discuss the many opportunities and challenges in the PCB design community, and what can be done to grow the numbers of PCB designers—and design instructors.
Embedded Design Techniques
Our expert contributors provide the knowledge this month that designers need to be aware of to make intelligent, educated decisions about embedded design. Many design and manufacturing hurdles can trip up designers who are new to this technology.
- Articles
- Columns
Search Console
- Links
- Events
||| MENU - design007 Magazine
Estimated reading time: 1 minute
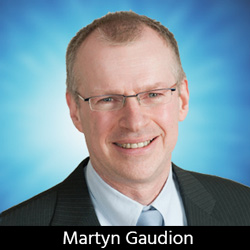
Impedance Control, Revisited
Surprising me on a regular basis is the way that demand for impedance control continues to extend into a broader range of product. After some 20 years of involvement in this field, I would have expected that everyone who needed to consider impedance control would have the capability nailed. Fortunately, that’s not the case, and a steady stream of “how to” questions keep coming my way.
The positives for new fabricators and designers lie in the fact that, even though impedance control may be new to them, there is a wealth of information available. Some of this information is common sense and some is a little counterintuitive. So, this month I’d like to go back to the fundamentals, and even if you are an experienced hand at the subject, it can be worth revisiting the basics from time to time.
Standards
It’s worth remembering that traceable reference impedance standards are available and all impedance measurement systems should be able to be compared to a traceable standard. The reference air line is the de facto standard for impedance—a precision manufactured coaxial standard “air” referring to the fact that air is employed as the dielectric in this type of precision reference line.
To read this entire article, which appeared in the May 2015 issue of The PCB Design Magazine, click here.
More Columns from The Pulse
The Pulse: Drilling Down on DocumentationThe Pulse: New Designer’s (Partial) Guide to Fabrication
The Pulse: Simplest Stackups Specified
The Pulse: Rough Roughness Reasoning
The Pulse: Industry Organizations Keep Knowledge Alive
The Pulse: Instilling an Informal Information Culture
The Pulse: Fitting Physics to Fact
The Pulse: Field Solver Finesse for Modelling Transmission Lines