-
- News
- Books
Featured Books
- design007 Magazine
Latest Issues
Current IssueLevel Up Your Design Skills
This month, our contributors discuss the PCB design classes available at IPC APEX EXPO 2024. As they explain, these courses cover everything from the basics of design through avoiding over-constraining high-speed boards, and so much more!
Opportunities and Challenges
In this issue, our expert contributors discuss the many opportunities and challenges in the PCB design community, and what can be done to grow the numbers of PCB designers—and design instructors.
Embedded Design Techniques
Our expert contributors provide the knowledge this month that designers need to be aware of to make intelligent, educated decisions about embedded design. Many design and manufacturing hurdles can trip up designers who are new to this technology.
- Articles
- Columns
Search Console
- Links
- Events
||| MENU - design007 Magazine
Estimated reading time: 2 minutes
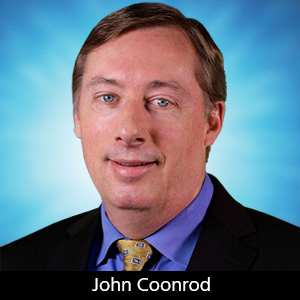
A Brief Overview of High-Frequency Laminates
The PCB laminates used for high-frequency applications possess several unique attributes that are distinctly different than FR-4 types of materials. Obviously, the electrical properties are better for high-frequency laminates than FR-4, however there are many other beneficial characteristics which may be less obvious for those unfamiliar with these specialty laminates. These other properties are the reason why sometimes, high-frequency laminates are used for applications that are not high-frequency.
Moisture absorption can be problematic for high-frequency circuits (and other applications) for several reasons. When a circuit absorbs moisture from its environment, some water content becomes part of the material matrix on a molecular level. Water has a high dielectric constant, with a value of approximately 70. Most components that make up a laminate have dielectric constant values in the range of about 2–10, so if an appreciable amount of the material matrix has a component of 70, the overall laminate dielectric constant will increase significantly. A change in dielectric constant will cause a change in impedance, propagation velocity, phase response and other circuit issues. Additionally, the change due to moisture is typically a variable based on the environmental conditions in which the circuit is operating.
The amount of moisture absorption that can impact circuit performance is unique to the circuit design and application. Some applications are nearly unaffected by moisture absorption issues and others will have electrical performance that is greatly affected. The amount of moisture absorption which is considered low for high-frequency applications is somewhat subjective, but as a general rule a value of 0.3% or less is considered good. Moisture absorption also increases insertion loss, and as another general rule, the applications that are higher frequency or higher speed are more susceptible to moisture effects.
Other issues that are critical to many high-frequency applications and also environment-related is TCDk and TCDf. All circuit materials have these attributes: TCDk is the temperature coefficient of dielectric constant (Dk) and TCDf is analogous in regards to dissipation factor (Df). Basically, this is the property of material which will change Dk or Df with a change in temperature. Many times this becomes an issue when an application is fine-tuned in a lab environment and it then performs different in the field as the temperature fluctuates. The amount that TCDk or TCDf impacts circuit performance is very design and application specific. Some applications will be unaffected by these changes and others may see dramatic shifts of electrical performance. An ideal TCDk or TCDf would be 0 ppm/°C, which gives no change in Dk or Df with a change in temperature, but this is typically not realistic. A general rule for a good TCDk is an absolute value of 70 ppm/°C; however, there are many applications which could tolerate 200 ppm/°C or even more.
To read this entire column, which appeared in the August 2015 issue of The PCB Design Magazine, click here.
More Columns from Lightning Speed Laminates
Lightning Speed Laminates: Millimeter-wave Properties and PCB Design ChallengesLightning Speed Laminates: Optimizing Thermal Management for Wireless Communication Systems
Lightning Speed Laminates: Test Vehicles for PCB Electrical Material Characterization
Lightning Speed Laminates: Optimum Thermal Stability Considerations
Lightning Speed Laminates: Thermal Management Isn’t Getting Easier
Lightning Speed Laminates: Benefits of High-Performance Hybrid Multilayer PCBs
Lightning Speed Laminates: An Overview of Copper Foils
Lightning Speed Laminates: The Importance of Circuit Features for Millimeter-Wave Applications