-
- News
- Books
Featured Books
- design007 Magazine
Latest Issues
Current IssueLevel Up Your Design Skills
This month, our contributors discuss the PCB design classes available at IPC APEX EXPO 2024. As they explain, these courses cover everything from the basics of design through avoiding over-constraining high-speed boards, and so much more!
Opportunities and Challenges
In this issue, our expert contributors discuss the many opportunities and challenges in the PCB design community, and what can be done to grow the numbers of PCB designers—and design instructors.
Embedded Design Techniques
Our expert contributors provide the knowledge this month that designers need to be aware of to make intelligent, educated decisions about embedded design. Many design and manufacturing hurdles can trip up designers who are new to this technology.
- Articles
- Columns
Search Console
- Links
- Events
||| MENU - design007 Magazine
The Bare (Board) Truth: The Top 10 Ways Designers Can Increase Profits
April 21, 2016 | Mark Thompson, Prototron CircuitsEstimated reading time: 2 minutes
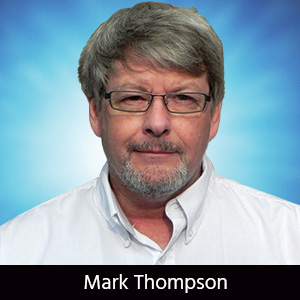
Some of you are probably wondering about the title of this article. “What could Mark possibly mean? How can a lowly PCB designer like me increase our company’s profits?”
So, can you truly increase profitability through PCB design practices? Yes, you can. And it starts with a philosophy that embraces DFM techniques. Then you must be ready for the initial release to a fabricator by ensuring that you are communicating all of your specifications and needs clearly to the fabrication house so that you get an accurate quote.
Let’s dive in, starting with Number 10 and working our way to the most important way a designer can increase company profits.
10. Accurate Fab Notes
I cannot over-stress this one. Lets talk about some common fab notes that can cause confusion, sometimes delaying your quote.
For instance, do copper weights refer to starting or finished weight? A standard note may read, “All copper weights listed on the stack-up detail are finished weights.” But a glance at the provided stack-up shows both 1 oz. inners and outers.
Remember, the first fab note specified FINISHED weights. This is not a problem for an internal layer, as they are “print and etch” for the most part. Their desired copper features are protected by the photosensitive resist and are simply printed, developed (to remove the resist not hardened by the light source), etched (to remove the unwanted metal) and resist stripped to remove the resist covering your desired copper features. So a 1 oz. callout for an inner layer is not at all uncommon.
The 1 oz. finish for the outer layers, however, is a bit unusual, given the fact that IPC recommends a minimum of 8/10 of a mil of plated copper on the surface and in the barrel of the hole for continuity. So starting on .5 oz. or even .25 oz. copper foils would mean we would have to plate less than what IPC recommends to finish at 1 oz.
The reality is that most fabricators err towards a full ounce or 1.4 mils of plating in the barrel and on the surface to meet that IPC minimum. That means starting on .25 oz. copper foil on the outers and plating up a full ounce results in 1.25 oz finish, which does not meet the drawing callout of 1 oz finished.
Worse yet, there may be impedance calculations that the customer has based on the 1 oz. finish for outer layers. Increasing the finished copper weight may mean a REDUCTION in your impedance lines. If you have already taken them down to .003” for instance, this may be a problem for the manufacturer.
This clarification about what is needed for desired copper can take additional time at the quote process. I am happy to say we are seeing more and more customers, both old and new, embracing this and creating non-conflicting manufacturing notes that allow for a 1 oz. additional plate.
To read this entire article, which appeared in the March issue of The PCB Design Magazine, click here.
Suggested Items
Designer’s Notebook: What Designers Need to Know About Manufacturing, Part 2
04/24/2024 | Vern Solberg -- Column: Designer's NotebookThe printed circuit board (PCB) is the primary base element for providing the interconnect platform for mounting and electrically joining electronic components. When assessing PCB design complexity, first consider the component area and board area ratio. If the surface area for the component interface is restricted, it may justify adopting multilayer or multilayer sequential buildup (SBU) PCB fabrication to enable a more efficient sub-surface circuit interconnect.
Insulectro’s 'Storekeepers' Extend Their Welcome to Technology Village at IPC APEX EXPO
04/03/2024 | InsulectroInsulectro, the largest distributor of materials for use in the manufacture of PCBs and printed electronics, welcomes attendees to its TECHNOLOGY VILLAGE during this year’s IPC APEX EXPO at the Anaheim Convention Center, April 9-11, 2024.
ENNOVI Introduces a New Flexible Circuit Production Process for Low Voltage Connectivity in EV Battery Cell Contacting Systems
04/03/2024 | PRNewswireENNOVI, a mobility electrification solutions partner, introduces a more advanced and sustainable way of producing flexible circuits for low voltage signals in electric vehicle (EV) battery cell contacting systems.
Heavy Copper PCBs: Bridging the Gap Between Design and Fabrication, Part 1
04/01/2024 | Yash Sutariya, Saturn Electronics ServicesThey call me Sparky. This is due to my talent for getting shocked by a variety of voltages and because I cannot seem to keep my hands out of power control cabinets. While I do not have the time to throw the knife switch to the off position, that doesn’t stop me from sticking screwdrivers into the fuse boxes. In all honesty, I’m lucky to be alive. Fortunately, I also have a talent for building high-voltage heavy copper circuit boards. Since this is where I spend most of my time, I can guide you through some potential design for manufacturability (DFM) hazards you may encounter with heavy copper design.
Trouble in Your Tank: Supporting IC Substrates and Advanced Packaging, Part 5
03/19/2024 | Michael Carano -- Column: Trouble in Your TankDirect metallization systems based on conductive graphite or carbon dispersion are quickly gaining acceptance worldwide. Indeed, the environmental and productivity gains one can achieve with these processes are outstanding. In today’s highly competitive and litigious environment, direct metallization reduces costs associated with compliance, waste treatment, and legal issues related to chemical exposure. What makes these processes leaders in the direct metallization space?