-
- News
- Books
Featured Books
- smt007 Magazine
Latest Issues
Current IssueBox Build
One trend is to add box build and final assembly to your product offering. In this issue, we explore the opportunities and risks of adding system assembly to your service portfolio.
IPC APEX EXPO 2024 Pre-show
This month’s issue devotes its pages to a comprehensive preview of the IPC APEX EXPO 2024 event. Whether your role is technical or business, if you're new-to-the-industry or seasoned veteran, you'll find value throughout this program.
Boost Your Sales
Every part of your business can be evaluated as a process, including your sales funnel. Optimizing your selling process requires a coordinated effort between marketing and sales. In this issue, industry experts in marketing and sales offer their best advice on how to boost your sales efforts.
- Articles
- Columns
Search Console
- Links
- Events
||| MENU - smt007 Magazine
JJS Stresses Need for Baking Prior to Flex Circuit Assembly
April 20, 2017 | Stephen Las Marias, I-Connect007Estimated reading time: 3 minutes
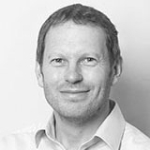
UK-based JJS Manufacturing is an EMS company that specializes in end-to-end procurement, manufacture (PCB assembly, box build, cabinet, electro-mechanical) and supply chain solutions. The company supplies complex, highly configurable, low-to-medium-volume industrial electronics products across a range of market sectors including industrial automation, process control, test and measurement, and laboratory technology.
Editor Stephen Las Marias spoke with Russell Poppe, director of technology, about the challenges of dealing with flex circuit assemblies and provides strategies to address them.
Stephen Las Marias: From your experience, what are the major challenges in flex circuit assembly?
Russell Poppe: From an assembly perspective, baking the flex circuits prior to manufacturing assembly is crucial as they can be susceptible to delamination. That said, baking any PCB prior to manufacturing is best practice and something we always do at JJS.
One of the biggest challenges in flex circuit assembly is making sure the circuits remain flat, particularly during the printing and pick-and-place processes. The parts of the circuit requiring SMT placement should have an FR-4 stiffener designed in underneath; but it is also important to work with the PCB supplier up front. Getting the panelization right is important so that the boards don’t bend when the parts are placed or when they pass through reflow. Panel design can be a challenge as flex circuits are often strange shapes! It might also be necessary to have a bespoke carrier or pallet to hold the flex circuits in place throughout the process; however, these carry additional costs—typically a few hundred pounds each.
Las Marias: What are the specific steps in a flexible circuit assembly process that have the biggest effect on yields?
Poppe: Failure to bake the flex circuits prior to assembly can lead to delamination issues. If panels are not kept flat during the pick and place process the SMT equipment can misplace components, leading to additional rework. Breaking out circuits from panels can also be an issue as often only thin layers of FR-4 are used, which can lead to damage if handled incorrectly.
Las Marias: How should these challenges be addressed?
Poppe: We would recommend working closely with the PCB supplier and perhaps investing in bespoke pallets or carriers. If the design is stable and the volumes are high enough, then the initial cost of the pallets might make sense. If your policy is to run standard oven profiles, then it’s likely that you will need to refine these—particularly if pallets are used as the oven profiles will vary significantly compared to a standard profile.
Las Marias: How different is the flex circuit assembly from the standard PCB assembly, and what are the important factors to consider?
Poppe: You could argue that the processes are very similar—providing you are already working to best practice! Care and attention should be given to panelization, circuits should be baked prior to assembly, and oven profiles should be tailored to suit the circuit being assembled. A robust NPI procedure should cover most of these points already.
Las Marias: Which end-applications are you seeing increasing use of flexible circuits?
Poppe: The demand for flex circuits in the sectors we serve—industrial electronics—is still relatively low. Clearly, there is much higher demand in automotive applications and consumer electronics, whether there is a significant increase in demand within the industrial sector remains to be seen.
Las Marias: When choosing an assembly partner for flex circuit assemblies/projects, what are the top things to consider?
Poppe: Robust NPI process; good material handling and preconditioning process prior to assembly (i.e., baking and dry storage; ensuring the manufacturer that you partner with is the right fit—that is, do they have demonstrable experience in producing similar products and flex circuits?) and design for manufacture support on PCBA.
Las Marias: Thank you, Russell.
Poppe: Thank you.
Suggested Items
Determining the Value-add of Box Build
04/24/2024 | Nolan Johnson, I-Connect007At a strategic level, adding box-building services makes sense for customer loyalty. But is it really that simple? Jon Schmitz, who manages customer engagement at RiverSide Integrated Solutions, talk about about what it really takes to be successful in offering EMS and final assembly services under the same company banner.
IMAPS & IPC to Host Onshoring Workshop
04/16/2024 | IPCThe International Microelectronics Assembly and Packaging Society (IMAPS) and IPC will host an Onshoring Workshop to discuss ongoing progress and forward-looking strategies to drive the Onshoring Advanced Packaging and Assembly, April 29 – May 1, 2024, in Arlington, Virginia.
IPC WinterCom 2024 Through the Eyes of One Dedicated Student
04/12/2024 | Sanjay Huprikar, IPCLauriane Testuz stands as a testament to the power of curiosity, perseverance, and the relentless pursuit of knowledge. Her story serves as a reminder that the path to success is often paved by an unwavering commitment to one's dreams.
2023: Year of Extremes for VDL Groep
04/08/2024 | VDL GroepThe year 2023 showed us two sides, with highs and lows. Low points were the passing of Wim van der Leegte in November, the reduction in the number of employees at VDL Nedcar and headwind in the Buses & Coaches division.
IPC, First and Only Organization in the Electronics Industry to Earn ANSI/ANAB Accreditation for Its Workforce Training
04/02/2024 | IPCIPC, the global leader in electronics education, announces a landmark achievement in professional education and training. Ten of IPC’s critical workforce training programs have been accredited by the ANSI National Accreditation Board (ANAB) under the stringent requirements of ANSI/ASTM E2659-18, Standard Practice for Certificate Programs.