-
- News
- Books
Featured Books
- smt007 Magazine
Latest Issues
Current IssueBox Build
One trend is to add box build and final assembly to your product offering. In this issue, we explore the opportunities and risks of adding system assembly to your service portfolio.
IPC APEX EXPO 2024 Pre-show
This month’s issue devotes its pages to a comprehensive preview of the IPC APEX EXPO 2024 event. Whether your role is technical or business, if you're new-to-the-industry or seasoned veteran, you'll find value throughout this program.
Boost Your Sales
Every part of your business can be evaluated as a process, including your sales funnel. Optimizing your selling process requires a coordinated effort between marketing and sales. In this issue, industry experts in marketing and sales offer their best advice on how to boost your sales efforts.
- Articles
- Columns
Search Console
- Links
- Events
||| MENU - smt007 Magazine
QFN Center Pads on PCBs
August 9, 2017 | Duane Benson, Screaming CircuitsEstimated reading time: 1 minute
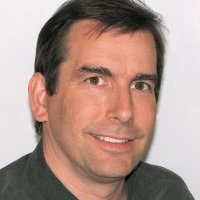
The QFN (quad-flat no-leads) package can no longer be considered exotic. It was about a decade ago, but not anymore. In fact, with the wafer scale BGA, it's one of the more common packages for new chip designs.
Not all QFNs come with an exposed metal pad underneath, but most do, and that can still cause problems with reflow solder. The pad itself isn't the problem, but improper solder paste stencil layer design can be.
The default stencil layer in the CAD library footprint might have an opening the full size of the metal pad. If that's the case, you'll need to modify the footprint so that you get 50-75 percent coverage with solder paste. If you don't, you may very well have yield problems. With a 100 percent open area, you'll most likely end up with too much solder in the middle. The part will ride up or float, and may not connect with all of the pads on the sides of the part.
The figure below shows a stencil with too large an opening in the center, a segmented paste layer in the CAD footprint, and the resultant segmented stencil. You may note that I said to shoot for 50-75 percent coverage and ask: "Well, is it 50 percent or 75 percent? What gives?"
True, that is a bit of ambiguity. However, anything in that range should be fine for prototype boards. If you're going for volume production, you'll want to work with your manufacturer to tweak the design for best high-volume yield.
Good news on this front is that many QFN manufacturers and parts library creators have taken notice of this. It's far more likely now than it was 10 years ago to find a datasheet correctly illustrating this, and footprints created correctly. But, always check your footprints to make sure.
Duane Benson is the Chief Technology Champion at Screaming Circuits, a prototype PCB assembly electronic manufacturing company in Canby, Oregon.
Suggested Items
Taiyo Circuit Automation Installs New DP3500 into Fuba Printed Circuits, Tunisia
04/25/2024 | Taiyo Circuit AutomationTaiyo Circuit Automation is proud to be partnered with Fuba Printed Circuits, Tunisia part of the OneTech Group of companies, a leading printed circuit board manufacturer based out of Bizerte, Tunisia, on their first installation of Taiyo Circuit Automation DP3500 coater.
Vicor Power Orders Hentec Industries/RPS Automation Pulsar Solderability Testing System
04/24/2024 | Hentec Industries/RPS AutomationHentec Industries/RPS Automation, a leading manufacturer of selective soldering, lead tinning and solderability test equipment, is pleased to announce that Vicor Power has finalized the purchase of a Pulsar solderability testing system.
AIM Solder’s Dillon Zhu to Present on Ultraminiature Soldering at SMTA China East
04/22/2024 | AIMAIM Solder, a leading global manufacturer of solder assembly materials for the electronics industry, is pleased to announce that Dillon Zhu will present on the topic: Ultraminiature Soldering: Techniques, Technologies, and Standards at SMTA China East. This event is being held at the Shanghai World Expo Exhibition & Convention Center from April 24-25.
AIM to Highlight NC259FPA Ultrafine No Clean Solder Paste at SMTA Wisconsin Expo & Tech Forum
04/18/2024 | AIMAIM Solder, a leading global manufacturer of solder assembly materials for the electronics industry, is pleased to announce its participation in the upcoming SMTA Wisconsin Expo & Tech Forum taking place on May 7 at the Four Points by Sheraton | Milwaukee Airport, in Milwaukee, Wisconsin.
Hentec/RPS Publishes an Essential Guide to Selective Soldering Processing Tech Paper
04/17/2024 | Hentec Industries/RPS AutomationHentec Industries/RPS Automation, a leading manufacturer of selective soldering, lead tinning and solderability test equipment, announces that it has published a technical paper describing the critical process parameters that need to be optimized to ensure optimal results and guarantee the utmost in end-product quality.