-
- News
- Books
Featured Books
- smt007 Magazine
Latest Issues
Current IssueSupply Chain Strategies
A successful brand is built on strong customer relationships—anchored by a well-orchestrated supply chain at its core. This month, we look at how managing your supply chain directly influences customer perception.
What's Your Sweet Spot?
Are you in a niche that’s growing or shrinking? Is it time to reassess and refocus? We spotlight companies thriving by redefining or reinforcing their niche. What are their insights?
Moving Forward With Confidence
In this issue, we focus on sales and quoting, workforce training, new IPC leadership in the U.S. and Canada, the effects of tariffs, CFX standards, and much more—all designed to provide perspective as you move through the cloud bank of today's shifting economic market.
- Articles
- Columns
- Links
- Media kit
||| MENU - smt007 Magazine
Training and Education: Key to Improving Electronics Assembly
August 16, 2017 | Stephen Las Marias, I-Connect007Estimated reading time: 15 minutes
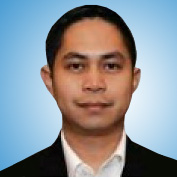
For this month's issue of SMT Magazine, we spoke with Luis Ramirez, COO, and Dan Prina, project manager of Lean enterprises and continuous improvement, at EMS firm MC Assembly to discuss the challenges of and strategies in improving the PCB assembly process from an EMS provider’s perspective. We also spoke with Manncorp's Tom Beck, director of marketing, and Chris Ellis, Eastern sales manager, to get their viewpoints on the subject as an equipment provider.
"From my perspective, from a management standpoint, first and foremost, improvement is a philosophy, and whatever you're doing today there’s always a better way to do it tomorrow. One of the biggest paradigms that we see across the industry is that one thing that may have worked in the past, we keep trying it and we keep trying it, and it may not work today because variables may have changed and the environment may have changed. That’s one of the biggest paradigms that, from a management standpoint in manufacturing, we have to remove, because what worked in the past not necessarily is going to work in the future," explains Ramirez. "For us, first we want to have a standard. We want to make sure that we partner with our suppliers of equipment and create standards so that we know when there is a problem, when there is an event that is outside a standard, it is easier to troubleshoot and easier to determine the root cause. Having said that, once you have a standard established, then you have to measure. You have to create a metric to understand whether or not you’re meeting your expected output out of that standard. With that measurement, then you are able to provide real-time feedback. That’s what drives a lot of the continuous improvement activities when we see trends. For example, when we look at the work that has been done in the previous day and we see a problem that keeps repeating that triggers a review, and triggers a team meeting or a kaizen event for the team to get together and figure out the root cause. What could be causing the problem and then second, what actions we could implement to eliminate or minimize the problem."
Ramirez notes that in today’s world of electronics, the PCBA real estate has become more and more critical. There are now a lot of low-profile BGAs. There are a lot of very small components that are all in very difficult areas inside a circuit board. "Even if you have great equipment, you still need to have that human intelligence that is able to figure out the right process to minimize any problem," Ramirez says.
He notes, though, that it does require having the equipment that is capable, but so is having the technical and the expertise and experience to be able to look at a problem and say, 'Yes, I know I can do A, B or C.'
"If you cannot figure it out, you should be able to pick up the phone and call the manufacturer of the equipment, call the manufacturer of the part, and even invite all of them and tell them, 'Hey, I’ve got this problem. How do you guys think we can solve it?' Again, sometimes what we think is a simple problem actually may require a very complex solution. In our world, there is no such thing as a simple problem," adds Ramirez.
One of the key measurements they base their improvements on is the overall cycle time. "Initially, what we wanted to do was to just feed it into our machines, we’ve always had a big focus on the technology of it. We’ve invested pretty heavily in some really good equipment. What we’ve found lately though is there’s a lot to be said for the simplicity," says Prina. "We definitely manage from a point where we look at running simulations and we know where our expected run times are on our equipment, but if you fail to manage the downtime, if you fail to manage the hand touch labor further on down the line, it can create a lot of problems. We have a phase-gate controlled process NPI release that goes step-by-step through the process. We try to identify what our problems are upfront but there’s certainly still quite a bit being done out on the floor once it’s released, and we go through that process. That’s when we try to get our operators engaged and getting that feedback from them, where we can minimize times lost, where we can engage some efficiency, and just getting that feedback back up to the PDM group to rewrite those processes or to engineering for review is really critical."
Do they go back to their customers and suggest some modifications for future revisions? Ramirez says they do. "As Dan explained, in a perfect world during the pre-production type run, there are a lot of these sins that should have been identified and, in theory, should have been corrected. What we’re finding is, in many cases, many of our customers’ development phase take more time than projected in their tollgate process to bring a product to life. They consume all the work for one reason or the other in the design phase to the point that by the time you want to prove your design, it’s way too late. In many instances, we are facing a situation in which the product has launched, even with a fault or deficiency we may have identified, because there is a pressure for that customer to launch a product," Ramirez explains. "We like to view ourselves as adding value to our customer. At MC, we’re going to do our best to provide you, based on your design, a good product. However, we’ve got to work together. We’ve got to be partners so that, at the end of the day, if we can improve your design and it's going to make our assembly process better, that is going to be an economical benefit for both companies. For the most part, most customers tend to take that feedback and in the next revision they fix it."
But he says they have other customers who are facing difficulty in changing the design because of third-party approvals or very long testing.
"Again, we have a mix of some that early in the process as we are doing the prototypes. We're able to provide feedback, which then they use to refine their design versus the other ones that they get the feedback but they realize that, 'Hey, I don't have the time.' It's going to be changed in the next revision. Then we have to live with that situation. Therefore, that's where it's critical to have all the controls that we put in place, like Dan was mentioning, we've got to figure out how to do it and how to do it well," says Ramirez.
Ellis agrees, saying that a lot of customers just don’t know how to design for manufacturability. "We often have to guide them so that their designs are consistent with their capabilities and available resources. For example, a customer may have a BOM with 175 different part numbers, which would necessitate multiple pick-and-place machines, when they really don’t have the budget for that. We can often assist them in designing their product in a way that meets the capability of equipment they can afford," he says.
Beck adds that many of their customers, especially the larger companies, will invest in their own prototyping equipment to be able to work out a lot of these issues in advance, before turning a product over to an assembler, who would produce the boards on a much larger scale when necessary.
Training and Education is Key
Overall, one of the key factors that these experts point to when it comes to improving the PCB assembly process is training and better education, as most of the people in the line just don’t have any formal training in electronics assembly methods.
Page 1 of 3
Testimonial
"Advertising in PCB007 Magazine has been a great way to showcase our bare board testers to the right audience. The I-Connect007 team makes the process smooth and professional. We’re proud to be featured in such a trusted publication."
Klaus Koziol - atgSuggested Items
Naprotek Appoints Mark Crebs to Lead Business Development for Products and Platforms
08/27/2025 | Naprotek LLCNaprotek, LLC, a leading provider of mission-critical electronics technology solutions, announced the appointment of Mark Crebs to Products and Platform Director of Business Development.
VVDN Expands Manufacturing Footprint into the UAE to Meet Global Demand
08/20/2025 | PRNewswireVVDN Technologies, a global provider of software, product engineering and electronics manufacturing services & solutions, today announced it is setting up a new manufacturing facility in the UAE as part of its global expansion strategy.
SisTech Manufacturing Expands Services: Leading Precision in Electronic Manufacturing
08/11/2025 | Globe NewswireSisTech Manufacturing, known for its expertise in precision electronic manufacturing services, is expanding what it can do in production. For over 30 years, the company has been recognized for its commitment to quality and its ability to meet the diverse demands of industries like aerospace and consumer electronics. With ISO 9001:2015 certification and ITAR registration,
Kaynes Circuits to Invest $570 Million in PCB Tech India’s Tamil Nadu State
08/07/2025 | I-Connect007 Editorial TeamKaynes Circuits India, a subsidiary of Kaynes Technology India, announced on Aug. 4 that it plans to invest roughly $570 million over the next six years in the southern state of Tamil Nadu, the Economic Times reported.
Technica to Host Demo Days Event August 13-14
08/04/2025 | Technica USATechnica USA is proud to announce its upcoming Demo Days Event, taking place August 13–14 at the company’s Demo Center in San Jose, California. The event will feature live demonstrations and presentations from key supply partners ESSEMTEC, INOVAXE, and PARMI showcasing the latest innovations in SMT manufacturing and automation technology.