-
- News
- Books
Featured Books
- smt007 Magazine
Latest Issues
Current IssueBox Build
One trend is to add box build and final assembly to your product offering. In this issue, we explore the opportunities and risks of adding system assembly to your service portfolio.
IPC APEX EXPO 2024 Pre-show
This month’s issue devotes its pages to a comprehensive preview of the IPC APEX EXPO 2024 event. Whether your role is technical or business, if you're new-to-the-industry or seasoned veteran, you'll find value throughout this program.
Boost Your Sales
Every part of your business can be evaluated as a process, including your sales funnel. Optimizing your selling process requires a coordinated effort between marketing and sales. In this issue, industry experts in marketing and sales offer their best advice on how to boost your sales efforts.
- Articles
- Columns
Search Console
- Links
- Events
||| MENU - smt007 Magazine
Top Five BGA Challenges to Overcome
October 9, 2017 | Bob Wettermann, BEST Inc.Estimated reading time: 4 minutes
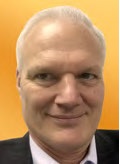
BGA component package dimensions continue to get thinner as more are being used in handheld device applications. End-use device requirements include the need to maintain their interconnections, even when dropped, thus necessitating underfill. The increased demand for higher board densities requires neighboring or mirrored devices during the rework process to be more challenging. Higher reflow temperatures of lead-free rework increases the pressure for properly shielding the neighboring components. These developments are causing BGA rework challenges. This summary will discuss the most challenging aspects of BGA rework and options for solutions.
1. Warped BGAs
Figure 1: Head-in-pillow defect.
One of the challenges in reworking BGAs at this time is the warping of the packages as ever thinner packages lead to a variety of problems. A largely noted issue of a warped BGA is the ‘Head in Pillow’ (HiP) defect (Figure 1). This defect may or may not be detectable during the X-Ray inspection. In this solder joint defect, the solder paste deposit will wet the pad, but does not fully wet the ball. This is due to the ball of the package being ‘pulled away’ during the device warping. The result is a solder joint with enough of a connection to have electrical integrity, but not sufficient mechanical strength.
Without the strength, these components may fail with a small amount of mechanical or thermal stress. This potentially costly defect is not usually detected in functional testing but rather in the field after the assembly has been exposed to some physical or thermal stresses. Warping can also cause bridging and shorts, at either the outer corners or the center of the device during replacement (Figure 2). This warping phenomenon can cause the center of the BGA to bow upwards and the corners down, or vice versa. Sometimes, this is enough to cause the corners to move closer to the circuit board surface. This puts extra pressure on the corner solder joints. Later in the lifecycle of the device, this may cause shorts or cracks.
There are several fine tunings of the rework process which will mitigate the impact of warped packages. The main way to lessen the impact of warping includes the adjustment of the reflow profile and solder paste chemistry. The reflow profile will help determine which areas of the device may be subject to thermal stress as well as ensuring the flux activity level does not expire. The solder paste chemistry is an integral step in making sure there is plenty of flux activity if the warping occurs over a prolonged reflow cycle. These variables are important to control during the BGA rework process to minimize warping.
Figure 2: Warpage and Z-height deflection on BGA.
By aiming for a very small temperature differential across the entire BGA package—less than 10°C across the entire package is optimal—the impact of device warpage can be greatly reduced in the rework process. One of the methods for ensuring a consistent and small temperature gradient across the entire package is to use a programmable multi-zone bottom-side heating source. Ideally, a multi-zoned heating source will heat the underside of the board to 100–120°C (lead-free processing temperatures) with the device location elevated to 140°C if the board and components can withstand this. This slight temperature differential will ensure that there is not undo thermal stress, which may delaminate or warp the board. The heating nozzle (assuming hot gas is used as the reflow source) will bring the solder balls up to 20–30°C above liquidus for 60–120 seconds.
In addition to the proper removal and reflow profile, the PCB will need to be properly supported to mitigate any effects of deflections on the PCB during the removal or reflow profiles. Board supports should be such that they prevent undue board deflections. The lack of support further exacerbates warping which may occur.
Solder paste chemistry can impact the degree to which the device or PCB is warped during the rework process. Solder pastes, with an activation system that can provide sustainable high-temperature fluxing, can create a homogenous connection. This connection goes beyond the ball and the paste alloy interface, which is important for warped devices to form an intermetallic bond. Those that are not able to sustain high-temperature efficacy are more prone to HiP defects.
2. Neighboring Device Damage
As the density of components on PCBs has increased, the need to protect neighboring temperature sensitive components near the BGA such as ceramic capacitors, crystals and plastic-bodied components such as connectors has increased. These devices must be protected from exposure to heat during the rework process. If they are not, they can become damaged showing either visible or ‘hidden’ damage. In addition, these components’ long-term reliability may be impacted by this heat exposure, even if their appearance does not show it. While these components may be able to withstand the peak temperature of 260°C (as defined in J-STD-002), there may be medium and long-term impacts to its reliability if the IMC layer grows too thick. Neighboring underfilled parts may have the material ‘ooze out’ as the softening point temperature is below the liquidus temperature of lead-free solder.
To read the full version of this article, which appeared in the September 2017 issue of SMT Magazine, click here.
Suggested Items
Taiyo Circuit Automation Installs New DP3500 into Fuba Printed Circuits, Tunisia
04/25/2024 | Taiyo Circuit AutomationTaiyo Circuit Automation is proud to be partnered with Fuba Printed Circuits, Tunisia part of the OneTech Group of companies, a leading printed circuit board manufacturer based out of Bizerte, Tunisia, on their first installation of Taiyo Circuit Automation DP3500 coater.
Vicor Power Orders Hentec Industries/RPS Automation Pulsar Solderability Testing System
04/24/2024 | Hentec Industries/RPS AutomationHentec Industries/RPS Automation, a leading manufacturer of selective soldering, lead tinning and solderability test equipment, is pleased to announce that Vicor Power has finalized the purchase of a Pulsar solderability testing system.
AIM Solder’s Dillon Zhu to Present on Ultraminiature Soldering at SMTA China East
04/22/2024 | AIMAIM Solder, a leading global manufacturer of solder assembly materials for the electronics industry, is pleased to announce that Dillon Zhu will present on the topic: Ultraminiature Soldering: Techniques, Technologies, and Standards at SMTA China East. This event is being held at the Shanghai World Expo Exhibition & Convention Center from April 24-25.
AIM to Highlight NC259FPA Ultrafine No Clean Solder Paste at SMTA Wisconsin Expo & Tech Forum
04/18/2024 | AIMAIM Solder, a leading global manufacturer of solder assembly materials for the electronics industry, is pleased to announce its participation in the upcoming SMTA Wisconsin Expo & Tech Forum taking place on May 7 at the Four Points by Sheraton | Milwaukee Airport, in Milwaukee, Wisconsin.
Hentec/RPS Publishes an Essential Guide to Selective Soldering Processing Tech Paper
04/17/2024 | Hentec Industries/RPS AutomationHentec Industries/RPS Automation, a leading manufacturer of selective soldering, lead tinning and solderability test equipment, announces that it has published a technical paper describing the critical process parameters that need to be optimized to ensure optimal results and guarantee the utmost in end-product quality.