-
- News
- Books
Featured Books
- smt007 Magazine
Latest Issues
Current IssueBox Build
One trend is to add box build and final assembly to your product offering. In this issue, we explore the opportunities and risks of adding system assembly to your service portfolio.
IPC APEX EXPO 2024 Pre-show
This month’s issue devotes its pages to a comprehensive preview of the IPC APEX EXPO 2024 event. Whether your role is technical or business, if you're new-to-the-industry or seasoned veteran, you'll find value throughout this program.
Boost Your Sales
Every part of your business can be evaluated as a process, including your sales funnel. Optimizing your selling process requires a coordinated effort between marketing and sales. In this issue, industry experts in marketing and sales offer their best advice on how to boost your sales efforts.
- Articles
- Columns
Search Console
- Links
- Events
||| MENU - smt007 Magazine
Saki to Demo AOI and SPI Systems at productronica
November 10, 2017 | Saki CorporationEstimated reading time: 2 minutes
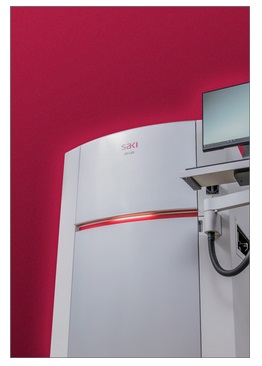
Saki Corporation, an innovator in the field of automated optical and x-ray inspection systems, will introduce its new 3Di AOI systems at productronica 2017, which will be held from November 14-17 in Munich, Germany. Saki will be in Stand A2.259.
The new system delivers high-speed (5,700mm2/sec), high-accuracy (XY positioning of 3µm at 3Ơ), height repeatability (below 2µm at 3Ơ), and scalable resolutions of 7, 12 and 18µm for boards weighing 12kg.
Saki's rigid gantry structure is a key component of the 3Di-LS2, 3Di-LD2, and 3Di-ZS2 hardware platforms. A dual-motor drive system, linear scale, and full closed-loop functionality provide machine accuracy and repeatability to generate absolute measurement data, which is essential for accurate machine-2-machine (M2M) communication. Saki's CoaXPress interface in the overhead camera captures images 1.7 times faster than previous models.
On display will also be Saki's new 3D solder paste inspection (SPI) systems, the 3Si-LS2, 3Si-LD2, and 3Si-7µm. One common software platform supports all Saki 3D inspection systems - solder paste, optical, and x-ray--with an easy-to-program, intuitive software wizard. Auto-programming software significantly reduces library creation time, as libraries are automatically created using Gerber and CAD data. Algorithm-based software provides extensive programming capabilities, even for non-programmers. Saki's inspection data and default thresholds adhere to IPC standards.
Saki is also introducing its new concept, Quality Driven Production, or QDP. QDP is a set of tools that ensures that the data and information that is communicated to third party systems is valid and accurate. It improves the stability of the process, while at the same time it increases productivity and minimizes the operating cost of the equipment. A self-diagnostic system with predictive and preventive maintenance management assures stable machine conditions and repeatable, consistent performance. Every key component is monitored along with system conditions, and a detailed diagnostic log is recorded. An optimized preventive maintenance plan reduces maintenance time, machine down-time, manpower, and costs.
The Multi Process View (MPV) on the BF2-Monitor shows the results of all inspection processes (SPI, pre-reflow, and post reflow) on one screen in real time for operator review, simplifying the verification process and making it less subject to error. It is also useful for analyzing the cause of a defective board.
"We are excited to introduce our new 3D AOI and 3D SPI systems to the industry at Productronica and to discuss our Smart Factory/Industry 4.0 initiatives and partnerships," said Katsuhiro Eddie Ichiyama, General Manager of SAKI Europe. "In addition to these systems, we will also be displaying Saki's 3D automated x-ray inspection (3D AXI) for circuit boards in applications that are too critical to fail."
About Saki
Since its inception in 1994, Saki has led the way in the development of automated recognition through robotic vision technology. Saki's 3D automated solder paste, optical, and x-ray inspection systems (SPI, AOI, AXI) have been recognized to provide the stable platform and advanced data capture mechanisms necessary for true M2M communication, improving production, process efficiency, and product quality. Saki Corporation has headquarters in Tokyo, Japan with offices, sales, and support centers around the world.
Suggested Items
Taiyo Circuit Automation Installs New DP3500 into Fuba Printed Circuits, Tunisia
04/25/2024 | Taiyo Circuit AutomationTaiyo Circuit Automation is proud to be partnered with Fuba Printed Circuits, Tunisia part of the OneTech Group of companies, a leading printed circuit board manufacturer based out of Bizerte, Tunisia, on their first installation of Taiyo Circuit Automation DP3500 coater.
Vicor Power Orders Hentec Industries/RPS Automation Pulsar Solderability Testing System
04/24/2024 | Hentec Industries/RPS AutomationHentec Industries/RPS Automation, a leading manufacturer of selective soldering, lead tinning and solderability test equipment, is pleased to announce that Vicor Power has finalized the purchase of a Pulsar solderability testing system.
AIM Solder’s Dillon Zhu to Present on Ultraminiature Soldering at SMTA China East
04/22/2024 | AIMAIM Solder, a leading global manufacturer of solder assembly materials for the electronics industry, is pleased to announce that Dillon Zhu will present on the topic: Ultraminiature Soldering: Techniques, Technologies, and Standards at SMTA China East. This event is being held at the Shanghai World Expo Exhibition & Convention Center from April 24-25.
AIM to Highlight NC259FPA Ultrafine No Clean Solder Paste at SMTA Wisconsin Expo & Tech Forum
04/18/2024 | AIMAIM Solder, a leading global manufacturer of solder assembly materials for the electronics industry, is pleased to announce its participation in the upcoming SMTA Wisconsin Expo & Tech Forum taking place on May 7 at the Four Points by Sheraton | Milwaukee Airport, in Milwaukee, Wisconsin.
Hentec/RPS Publishes an Essential Guide to Selective Soldering Processing Tech Paper
04/17/2024 | Hentec Industries/RPS AutomationHentec Industries/RPS Automation, a leading manufacturer of selective soldering, lead tinning and solderability test equipment, announces that it has published a technical paper describing the critical process parameters that need to be optimized to ensure optimal results and guarantee the utmost in end-product quality.