-
- News
- Books
Featured Books
- smt007 Magazine
Latest Issues
Current IssueBox Build
One trend is to add box build and final assembly to your product offering. In this issue, we explore the opportunities and risks of adding system assembly to your service portfolio.
IPC APEX EXPO 2024 Pre-show
This month’s issue devotes its pages to a comprehensive preview of the IPC APEX EXPO 2024 event. Whether your role is technical or business, if you're new-to-the-industry or seasoned veteran, you'll find value throughout this program.
Boost Your Sales
Every part of your business can be evaluated as a process, including your sales funnel. Optimizing your selling process requires a coordinated effort between marketing and sales. In this issue, industry experts in marketing and sales offer their best advice on how to boost your sales efforts.
- Articles
- Columns
Search Console
- Links
- Events
||| MENU - smt007 Magazine
PCB Pad Repair Techniques
January 8, 2018 | Bob Wettermann, BEST Inc.Estimated reading time: 3 minutes
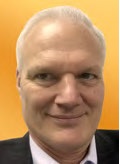
There are a variety of reasons behind pads getting "lifted" completely or partially from the laminate of a PCB. Per the just revised IPC-A-610 Revision G, a defect for all three classes occurs when the land is lifted up one or more pad thicknesses. Lifted pads can occur when a device has been improperly removed or there is a manufacturing defect in the board construction. The propensity for this to occur when pads are very small, like in the case of an 0201 or when there is an unconnected BGA pad.
In any case, as with any repair, the ultimate decision on the ability to repair the pad lies with the customer. In some cases, only a limited number of repairs are allowed by the customer and if allowed the same repairs can only be attempted with customer-approved materials and methods. Like all repairs defined by the IPC 7711/21 Rework of Electronic Assemblies/Repair and Modification of Printed Boards and Electronic Assemblies, the repairs can only be done with customer approval.
Figure 1: Initial damaged pad requiring replacement.
There are two different industry-accepted repair techniques for lifted pads when the objective is to replace the pad. One involves the use of dry film heat and pressure curable adhesive that is stuck to the replacement pad. The second involves the use of a two-part epoxy and “gluing” the replacement pad to the laminate. While the better method usually involves personal preferences, pull test data and better observed results of the replacement pad staying in position post soldering makes the epoxy method the one of choice.
The epoxy repair technique outlined in IPC-7721 Rev C Procedure 4.7.1, describes a method for the repair of pads by using a replacement plated pad (attached via a skeleton of other patterns) and a two-part epoxy adhesive system. Each of the steps in the process require cleaning for best possible adherence of the repair materials as well as well as for inspection to make sure that the procedure is done properly. To start, remove the pad with a sharp knife and carefully cut a small piece of the connecting circuit.
Figure 2: Replacement pads of commercial circuit frame.
Using the proper solder and flux, attach the replacement pad with the connecting circuit by lap soldering the two together. Mix the two-part epoxy per the manufacturer’s suggestions, direct the mixture and apply pressure to the replacement pad and laminate and cure per the manufacturer’s instructions. (This technique also works for still attached but lifted only pads.) Make sure to inspect for anomalies and perform an electrical continuity test as a post repair check.
In a second repair method (IPC 7721 Procedure 4.7.2), a dry film-backed plated replacement pad is adhered to the PCB laminate by a heat and pressure-activated dry film. All the process steps in the above epoxy method apply until you get to the sequence where a repair material is chosen. Once the replacement pad in the circuit frame is identified, it is cut out from the frame using a sharp blade. Only in this case the technician has to make sure that they cut through both the replacement pad as well as the adhesive backing. Now the pad is soldered to the trace if required.
Figure 3: Replacement pad held down with Kapton tape for epoxy/resin curing process.
A special tip and handheld heating tool similar to a soldering iron is placed into a fixture which controls the downward pressure. Through this heated tip temperature and tip pressure the adhesive cures. The other steps are similar in nature to the epoxy repair method.
One of the most challenging types of pad repair are those with embedded vias. These vias, connected to other board layers, will still need to maintain their connectivity to the connected layer post repair. There are numerous approaches to maintaining these very difficult repairs including but not limited to small jumper wires of small copper trace interconnections.
There are two methods for repairing damaged pads. Both the two-part epoxy/resin and the dry film techniques will do the job. In either event, a highly-skilled and trained technician can make most of these types of repairs when financially viable and where the risks of reliability have been mitigated based on the end use operating environment.
Reference
1. IPC 7711/21 Rework of Electronic Assemblies/Repair and Modification of Printed Boards and Electronic Assemblies.
Suggested Items
Taiyo Circuit Automation Installs New DP3500 into Fuba Printed Circuits, Tunisia
04/25/2024 | Taiyo Circuit AutomationTaiyo Circuit Automation is proud to be partnered with Fuba Printed Circuits, Tunisia part of the OneTech Group of companies, a leading printed circuit board manufacturer based out of Bizerte, Tunisia, on their first installation of Taiyo Circuit Automation DP3500 coater.
Vicor Power Orders Hentec Industries/RPS Automation Pulsar Solderability Testing System
04/24/2024 | Hentec Industries/RPS AutomationHentec Industries/RPS Automation, a leading manufacturer of selective soldering, lead tinning and solderability test equipment, is pleased to announce that Vicor Power has finalized the purchase of a Pulsar solderability testing system.
AIM Solder’s Dillon Zhu to Present on Ultraminiature Soldering at SMTA China East
04/22/2024 | AIMAIM Solder, a leading global manufacturer of solder assembly materials for the electronics industry, is pleased to announce that Dillon Zhu will present on the topic: Ultraminiature Soldering: Techniques, Technologies, and Standards at SMTA China East. This event is being held at the Shanghai World Expo Exhibition & Convention Center from April 24-25.
AIM to Highlight NC259FPA Ultrafine No Clean Solder Paste at SMTA Wisconsin Expo & Tech Forum
04/18/2024 | AIMAIM Solder, a leading global manufacturer of solder assembly materials for the electronics industry, is pleased to announce its participation in the upcoming SMTA Wisconsin Expo & Tech Forum taking place on May 7 at the Four Points by Sheraton | Milwaukee Airport, in Milwaukee, Wisconsin.
Hentec/RPS Publishes an Essential Guide to Selective Soldering Processing Tech Paper
04/17/2024 | Hentec Industries/RPS AutomationHentec Industries/RPS Automation, a leading manufacturer of selective soldering, lead tinning and solderability test equipment, announces that it has published a technical paper describing the critical process parameters that need to be optimized to ensure optimal results and guarantee the utmost in end-product quality.