-
- News
- Books
Featured Books
- pcb007 Magazine
Latest Issues
Current IssueThe Growing Industry
In this issue of PCB007 Magazine, we talk with leading economic experts, advocacy specialists in Washington, D.C., and PCB company leadership to get a well-rounded picture of what’s happening in the industry today. Don’t miss it.
The Sustainability Issue
Sustainability is one of the most widely used terms in business today, especially for electronics and manufacturing but what does it mean to you? We explore the environmental, business, and economic impacts.
The Fabricator’s Guide to IPC APEX EXPO
This issue previews many of the important events taking place at this year's show and highlights some changes and opportunities. So, buckle up. We are counting down to IPC APEX EXPO 2024.
- Articles
Article Highlights
- Columns
Search Console
- Links
- Events
||| MENU - pcb007 Magazine
Entering—and Enjoying—the Industry
February 13, 2018 | Jonathan Zinski, I-Connect007Estimated reading time: 6 minutes
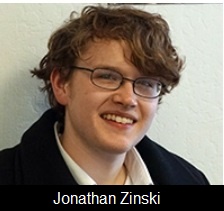
I was recently given the opportunity to write an article for our publication. Being somewhat new to this industry, I figured it would be a good idea to write an introduction on how I got into electronics—specifically the part most people my age don’t give thought to.
I remember the moment I first saw a printed circuit board. It was cold outside during Christmas at my grandma’s house, but the house was warm and full of friends and family. I was around age six or seven, a very curious kid, and we each had our own stack of presents scattered throughout the living room. When I opened one of my presents to find a Game Boy Color, a handheld video game, I was ecstatic! I immediately noticed the purple translucent case because I could see what was underneath it—a small green board. That’s when my dad said, “PCBs,” the acronym that defines our industry. I gave it little thought at the time, but that moment left a lasting impression.
Years later, my middle school technology class had an interesting learning structure with various booths and projects students would work on for a week. Stations included activities such as sewing, a CAD CNC machine that etched artwork onto plastic, a flight simulator, and the most popular, a booth where you could make a professional pen out of blocks of wood. As a kid, the choice was a difficult one for me; many students had already run over to the coolest-looking booths.
After carefully examining my options, I chose the one that reminded me of my Game Boy Color (which I still have to this day). The booth featured a soldering station with a kit to make a small blinking device with red and white LEDs. The idea of holding a hot iron inches away from my body that could turn solid metal into liquid was a bit unnerving, but I decided to take the plunge. The first section of the station involved watching short videos about series and parallel circuits, resistance, and safety. I was fascinated to learn that tree sap was part of the magic of solder and I had a blast putting together the board components. I fiddled with it all day and I even had a component fall off, so I tried to bypass the connection. Despite receiving some odd looks on the school bus at the end of the day, the whole experience, especially the blinking gizmo, left an impression that influenced me for years to come.
Caption: The original Game Boy Color, still in my possession.
Jumping to 2015, after finishing technical school in San Francisco and meeting the girl of my dreams, I moved into a cozy (extremely tiny) apartment in a hip (stupidly expensive) part of the city. I worked at a popular ice cream/chocolate shop in Ghirardelli Square. Gradually, life started to become a little repetitious; it was time to stretch myself in a new direction. My roommate suggested I check out a local hackerspace called Noisebridge. They had a weekly event called “Circuit Hacking Monday,” which turned out to be a class on soldering and putting together kits. It was a short bike ride away, so I decided to check it out.
The class was led by Mitch Altman, a man best known for inventing the TV-B-Gone—a device that functions as a universal remote and can turn off any TV from anywhere. He was extremely passionate about teaching others, especially young people, about electronics. Mitch included the TV-B-Gone in the various kits he brought for the class and it’s the one I chose to assemble. I had such a good time at this event. The smell of the rosin was nostalgically familiar to me and reminded me of my past interactions with electronics, solder, and PCBs.
I became more active at Noisebridge and attended whenever I had time. I loved digging through the e-waste bin and would disassemble any electronics I found. I even found an old retro-looking battery charger that I took apart and fixed, although fixing might not be exactly right—I simply bypassed a safety fuse that had blown.
Making the wires from an old hair dryer glow with the repaired battery charger.
Because I was interested in chemistry as much as electronics, I once took apart some lithium ion batteries for the metal inside. I had the proper gear on (i.e., ventilator, gloves, etc.) and planned to walk outside to remove the inner core of the battery. However, I failed to notify everyone else in the space of what I was doing. I’m not sure what kind of gas was released, but before I even completely removed the core, a very weird smell drifted through the room—almost sweet and fruity. When people started asking about the smell, I knew I needed to head outside. I have some other stories, but I’d rather not go into my youthful disregard for safety. Even with occasional trouble, the space was an amazing resource for me.
Eventually, I wanted to make something electronic of my own. I had an interest in renewable energy, especially drawing power from easily accessible sources. One day, I stumbled upon Peltier tiles and started investigating thermoelectrics. I found information online about low-voltage Joule Thieves and started working on a circuit that could generate enough charge to light up LEDs just from body heat. My idea was to put it into a bike helmet. The Joule Thief had a toroidal transformer core that I hand wound—100 turns in one direction and four in the other. Hand winding those small ferrite rings only made me more appreciative of the machines we have in this industry. Being a novice, it was a spectacular feeling when I got everything hooked up correctly and the lights turned on.
During this time, I still worked at the Ghirardelli ice cream/chocolate shop as a “chocolatier.” The tourist traffic never ended, and I was the guy handing out chocolate to everyone who walked in. I talked to people from all around the world. We rarely experienced unhappy customers because most people were on vacation, and after all, I was handing them free chocolate.
One fateful day, Barry Matties of I-Connect007 walked into the Ghirardelli store. We struck up a great conversation, and when we got on the subject of electronics, I enthusiastically shared my helmet project and the plans I had. We stayed in contact, and he even connected me to a local electronics manufacturer who could help me when I was ready to get my design turned into a finished PCB. Little did I know this would be my entrance into the PCB industry. A few months later, Barry hired me.
I may not have a formal education in this specific sector, but I-Connect007 has given me opportunities to learn and I’ve tried to take advantage of that. I did not grow up in the industry, but I certainly feel adopted.
I plan to keep writing about my experiences, both past and current, and about new technology trends affecting our market, such as the ever-growing 3D printing applications and their rapid advancements, which stand to benefit our industry. And of course, I’d like to give a perspective on this industry from my age group.
Until then, thanks for reading.
Additional Read:
Suggested Items
Taiyo Circuit Automation Installs New DP3500 into Fuba Printed Circuits, Tunisia
04/25/2024 | Taiyo Circuit AutomationTaiyo Circuit Automation is proud to be partnered with Fuba Printed Circuits, Tunisia part of the OneTech Group of companies, a leading printed circuit board manufacturer based out of Bizerte, Tunisia, on their first installation of Taiyo Circuit Automation DP3500 coater.
Vicor Power Orders Hentec Industries/RPS Automation Pulsar Solderability Testing System
04/24/2024 | Hentec Industries/RPS AutomationHentec Industries/RPS Automation, a leading manufacturer of selective soldering, lead tinning and solderability test equipment, is pleased to announce that Vicor Power has finalized the purchase of a Pulsar solderability testing system.
AIM Solder’s Dillon Zhu to Present on Ultraminiature Soldering at SMTA China East
04/22/2024 | AIMAIM Solder, a leading global manufacturer of solder assembly materials for the electronics industry, is pleased to announce that Dillon Zhu will present on the topic: Ultraminiature Soldering: Techniques, Technologies, and Standards at SMTA China East. This event is being held at the Shanghai World Expo Exhibition & Convention Center from April 24-25.
AIM to Highlight NC259FPA Ultrafine No Clean Solder Paste at SMTA Wisconsin Expo & Tech Forum
04/18/2024 | AIMAIM Solder, a leading global manufacturer of solder assembly materials for the electronics industry, is pleased to announce its participation in the upcoming SMTA Wisconsin Expo & Tech Forum taking place on May 7 at the Four Points by Sheraton | Milwaukee Airport, in Milwaukee, Wisconsin.
Hentec/RPS Publishes an Essential Guide to Selective Soldering Processing Tech Paper
04/17/2024 | Hentec Industries/RPS AutomationHentec Industries/RPS Automation, a leading manufacturer of selective soldering, lead tinning and solderability test equipment, announces that it has published a technical paper describing the critical process parameters that need to be optimized to ensure optimal results and guarantee the utmost in end-product quality.