-
- News
- Books
Featured Books
- smt007 Magazine
Latest Issues
Current IssueBox Build
One trend is to add box build and final assembly to your product offering. In this issue, we explore the opportunities and risks of adding system assembly to your service portfolio.
IPC APEX EXPO 2024 Pre-show
This month’s issue devotes its pages to a comprehensive preview of the IPC APEX EXPO 2024 event. Whether your role is technical or business, if you're new-to-the-industry or seasoned veteran, you'll find value throughout this program.
Boost Your Sales
Every part of your business can be evaluated as a process, including your sales funnel. Optimizing your selling process requires a coordinated effort between marketing and sales. In this issue, industry experts in marketing and sales offer their best advice on how to boost your sales efforts.
- Articles
- Columns
Search Console
- Links
- Events
||| MENU - smt007 Magazine
Conversation with Miraco… Strategies for Successful Flex Circuit Assembly
July 11, 2018 | Stephen Las Marias, I-Connect007Estimated reading time: 3 minutes
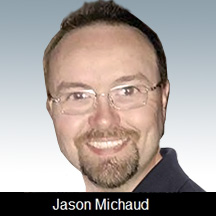
Miraco Inc. offers design, sourcing and value-added assembly of flexible interconnect products, including flex circuits, flat cables and wire/cable assemblies. The company services its diverse customer base from multiple locations—including headquarters in Manchester, New Hampshire, and its principal manufacturing site, Miraco South facility, in Tijuana, Mexico. The company also has additional satellite offices in the north and southeastern parts of the United States.
Jason Michaud, a 19-year veteran at Miraco, is the company’s new vice president of sales. In an interview with SMT007 Magazine, Jason speaks about the challenges in flex circuit assembly, and the best practices to address those issues.
Stephen Las Marias: Are you seeing increasing demand for flexible circuits?
Jason Michaud: Yes, with packaging sizes getting smaller, the need for creative flex solutions is growing. Overall, we are seeing an increase in demand for flexible printed circuits.
Las Marias: What factors are driving this?
Michaud: What’s driving a good portion of new business for Miraco is the redesign and sourcing of flexible printed circuits for customers who had gone directly offshore with their flexible circuit requirements previously and have experienced problems doing so. We are seeing a lot of flex circuits that were underdesigned or improperly designed to meet their intended use.
Las Marias: What are the top three challenges when it comes to flexible circuit assembly?
Michaud: The challenge for flexible circuit assembly is balancing electrical, mechanical, environmental and cost requirements with the material availability of suppliers and the manufacturability of the complete interconnect system. Pressure sensitive adhesive is a good example of something that is simple in relative terms compared to the flexible circuit layers; however, it drastically complicates the assembly process by limiting handling and cleaning options post soldering. However, if you process the soldering and cleaning of the assembly first, it is labor intensive and costly to apply the pressure-sensitive adhesive in piece form. It’s a double-edged sword.
Las Marias: Which parts of the assembly process are greatly impacted when doing flex circuit assemblies?
Michaud: When considering assembly, panelization and fixturing during design become important, as to panel size and panel stability. The number and type of components will dictate these parameters. These are important to facilitate the proper oven location during reflow. Oversized panels or unstable panels can greatly affect reflow and profile results in turn affecting yield and cost. Singulation post assembly is always a concern that is flexible circuit- and component-specific.
Las Marias: What strategies do you employ to address these challenges?
Michaud: Understanding the capabilities of the assembly equipment and its limitations is vital. Having calibrated equipment and a known repeatable process is key. Outlining post assembly can be accomplished through steel rule die, hard punch dies or lasering. Depending on the components that are assembled, the number you are outlining, and the required outline tolerance determine the best and most cost-effective route.
Las Marias: How different is the assembly of flex circuits from rigid- or rigid-flex circuits? What are the critical factors to consider?
Michaud: Flex circuits are typically more sensitive to assembly processes than their rigid-flex counterparts. In either case, as both products are hydroscopic, pre-bake cycles are a critical precursor to any assembly. In flex assembly, consideration must be given to added support for solder pad and/or through-hole areas with stiffening materials, preventing stress from transitioning to the soldered joint as, of course, flex circuits want to flex. In rigid-flex, you are more typically assembling to the rigid area and it provides self-stress relief. Proper pad sizing and thermal relief during design helps optimize reflow and hand solder assembly.
To read the full version of this article, which appeared in the June 2018 issue of SMT007 Magazine, click here.
Suggested Items
Taiyo Circuit Automation Installs New DP3500 into Fuba Printed Circuits, Tunisia
04/25/2024 | Taiyo Circuit AutomationTaiyo Circuit Automation is proud to be partnered with Fuba Printed Circuits, Tunisia part of the OneTech Group of companies, a leading printed circuit board manufacturer based out of Bizerte, Tunisia, on their first installation of Taiyo Circuit Automation DP3500 coater.
Vicor Power Orders Hentec Industries/RPS Automation Pulsar Solderability Testing System
04/24/2024 | Hentec Industries/RPS AutomationHentec Industries/RPS Automation, a leading manufacturer of selective soldering, lead tinning and solderability test equipment, is pleased to announce that Vicor Power has finalized the purchase of a Pulsar solderability testing system.
AIM Solder’s Dillon Zhu to Present on Ultraminiature Soldering at SMTA China East
04/22/2024 | AIMAIM Solder, a leading global manufacturer of solder assembly materials for the electronics industry, is pleased to announce that Dillon Zhu will present on the topic: Ultraminiature Soldering: Techniques, Technologies, and Standards at SMTA China East. This event is being held at the Shanghai World Expo Exhibition & Convention Center from April 24-25.
AIM to Highlight NC259FPA Ultrafine No Clean Solder Paste at SMTA Wisconsin Expo & Tech Forum
04/18/2024 | AIMAIM Solder, a leading global manufacturer of solder assembly materials for the electronics industry, is pleased to announce its participation in the upcoming SMTA Wisconsin Expo & Tech Forum taking place on May 7 at the Four Points by Sheraton | Milwaukee Airport, in Milwaukee, Wisconsin.
Hentec/RPS Publishes an Essential Guide to Selective Soldering Processing Tech Paper
04/17/2024 | Hentec Industries/RPS AutomationHentec Industries/RPS Automation, a leading manufacturer of selective soldering, lead tinning and solderability test equipment, announces that it has published a technical paper describing the critical process parameters that need to be optimized to ensure optimal results and guarantee the utmost in end-product quality.