-
- News
- Books
Featured Books
- pcb007 Magazine
Latest Issues
Current IssueThe Growing Industry
In this issue of PCB007 Magazine, we talk with leading economic experts, advocacy specialists in Washington, D.C., and PCB company leadership to get a well-rounded picture of what’s happening in the industry today. Don’t miss it.
The Sustainability Issue
Sustainability is one of the most widely used terms in business today, especially for electronics and manufacturing but what does it mean to you? We explore the environmental, business, and economic impacts.
The Fabricator’s Guide to IPC APEX EXPO
This issue previews many of the important events taking place at this year's show and highlights some changes and opportunities. So, buckle up. We are counting down to IPC APEX EXPO 2024.
- Articles
- Columns
Search Console
- Links
- Events
||| MENU - pcb007 Magazine
Flex Time: Why is Rigid-Flex So Expensive?
July 11, 2018 | Bob Burns, PRINTED CIRCUITSEstimated reading time: 1 minute
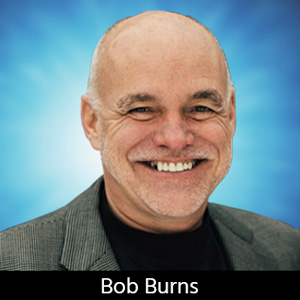
One question that I hear fairly often, particularly after an initial quotation, is “Why is rigid-flex so expensive?” In this article, I’ll share with you the cost drivers in rigid-flex relative to standard rigid boards and flex circuits with stiffeners. A typical rigid-flex PWB will cost about seven times the cost of the same design on a hard board, and two to three times an equivalent flex circuit with stiffeners. A good way to estimate the cost of rigid-flex board in low-level production quantities is 35 to 40 cents per square inch, per layer. So, if you have an eightlayer board that measures 4” x 6”, your costing would look like this:
8 layers x 4” x 6” x $0.40/sq.in. = $ 76.80 each
Again, this applies only to low level production quantities. This is a helpful calculation for getting a quick, rough idea of what your part might cost as a rigid-flex. Rigid-flex PWBs cost quite a bit more, primarily because of the higher cost of the raw materials we use to build them, relative to standard rigid boards or even flex boards. The number one cost driver is the no-flow prepreg. Rigid-flex manufacturers have to use no-flow, or sometimes low-flow prepreg, so that the resin does not flow out onto the flexible areas of the board. No-flow prepregs are designed to offer just enough flow to fill the circuits in the hardboard areas, but not enough to flow out onto the flexible areas of the boards.
No-flow and low-flow prepregs run from $1.50 to $3 per square foot. Conventional rigid board high-flow prepregs run around $.25 per square foot, so there is a large differential in price just for the prepreg. A couple of other things contribute to the cost as well. No-flow prepreg is only available in 1080 and 106 glass cloth styles, which typically press out at .0025” and .002” respectively, so they are thin. Rigid-flex manufacturers don’t have 2113, 2116, 7628 glass styles available to manufacture your board. It is wise to use two plies of prepreg between layers within your construction. The no-flow resin resists flowing, so to assure adequate fill, we use two plies of prepreg between each layer.
To read the full version of this article which appeared in the April 2018 issue of Flex007 Magazine, click here.
Suggested Items
Real Time with... IPC APEX EXPO 2024: Sustainability in the Industry
04/26/2024 | Real Time with...IPC APEX EXPOGuest Editor Henry Crandall and Chris Nash of Indium Corporation discuss the company's 90th anniversary and its focus on sustainability. They focus on the benefits of sustainable materials, their compatibility, and value propositions. The conversation also highlights how Durafuse LT technology's role in reducing reflow temperatures is leading to significant cost and energy savings. Nash also touches on downstream sustainability efforts such as using recycled materials for packaging.
Book Excerpt: The Printed Circuit Assembler’s Guide to... Factory Analytics
04/24/2024 | I-Connect007 Editorial TeamIn our fast-changing, deeply competitive, and margin-tight industry, factory analytics can be the key to unlocking untapped improvements to guarantee a thriving business. On top of that, electronics manufacturers are facing a tremendous burden to do more with less. If you don't already have a copy of this book, what follows is an excerpt from the introduction chapter of 'The Printed Circuit Assembler’s Guide to... Factory Analytics: Unlocking Efficiency Through Data Insights' to whet your appetite.
Ark Electronics Expands Global Manufacturing Factory Network in North America and Europe
04/17/2024 | PRNewswireElectronic Manufacturing Company Ark Electronics recently announced the expansion of its Global Factory Network with the addition of Electronics Manufacturing Service (EMS) capabilities in Mexico and Europe.
Microchip Technology Acquires Neuronix AI Labs
04/16/2024 | Microchip Technology Inc.Innovative technology enhances AI-enabled intelligent edge solutions and increases neural networking capabilities.
Fluor Awarded U.S. Air Force Contract Augmentation Program V Task Order for Tinian
04/11/2024 | BUSINESS WIREFluor Corporation announced that the U.S. Air Force Installation Contracting Agency awarded the company a task order contract for Pavement and Transportation Support North Field, Tinian, Commonwealth of the Northern Mariana Islands (CNMI).