-
- News
- Books
Featured Books
- smt007 Magazine
Latest Issues
Current IssueBox Build
One trend is to add box build and final assembly to your product offering. In this issue, we explore the opportunities and risks of adding system assembly to your service portfolio.
IPC APEX EXPO 2024 Pre-show
This month’s issue devotes its pages to a comprehensive preview of the IPC APEX EXPO 2024 event. Whether your role is technical or business, if you're new-to-the-industry or seasoned veteran, you'll find value throughout this program.
Boost Your Sales
Every part of your business can be evaluated as a process, including your sales funnel. Optimizing your selling process requires a coordinated effort between marketing and sales. In this issue, industry experts in marketing and sales offer their best advice on how to boost your sales efforts.
- Articles
- Columns
Search Console
- Links
- Events
||| MENU - smt007 Magazine
Is Component Testing Using ROSE Practical?
September 6, 2018 | Joe Russeau, Precision Analytical Laboratory, and Mark Northrup, IEC ElectronicsEstimated reading time: 3 minutes
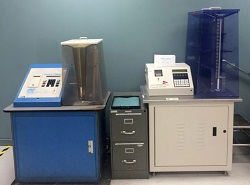
In a previous article, "It's Time to Retire ROSE Testing," we discussed the basis for why ROSE testing should be retired as an industry cleanliness or process control test. In this article, we reemphasize our position by highlighting some work we presented at the 2017 SMTA International Conference comparing component cleanliness results from the Resistivity of Solvent Extract (ROSE) against Ion Chromatography (IC) results. For those of you interested in reviewing that body of work, the working title was "PCBA Component Cleanliness Specifications Limits are Lacking."
The ROSE test has been used in the electronics industry since the early 1970s. It was originally developed to estimate the amount of residual rosin flux remaining on a printed board. The predominant flux from that era contained greater than 30% rosin. So, it should go without saying that modern day flux technology and circuit designs are vastly different from those 70s-era predecessors. By that same token, our methods for assessing the ionic cleanliness of printed board assemblies are vastly different as well, right? Well, not exactly. The ROSE test is still the most predominantly used ionic cleanliness test in our industry and in truth, it has not been modified or changed since the early 1980s. In addition, ROSE testing is not only used for determining the ionic cleanliness of printed boards and printed board assemblies, but it is also being used for evaluating the cleanliness of components.
In the previous article, Mark and I indicated that there were two important attributes necessary for evaluating the ionic cleanliness of PCBs and PCBAs. These attributes would be considerably more crucial for evaluating components. We said that those two attributes were selectivity and sensitivity. To properly evaluate ionic cleanliness, it is important to use as little extraction solvent as possible (to concentrate the residues to the area being evaluated) and to have a system that can identify each specific residue that is present. The ROSE test provides a single bulk value (not ion selective) and liters of solution are often used, which affects the sensitivity. Please consider the results in the following table taken from our 2017 SMTAi presentation.
Figure 1: IC has considerably greater selectivity than does ROSE and can identify specific ion species from a sample extract.
Before I discuss the results in Figure 1, it would be prudent to first discuss what was done. First, the cleanliness of five different ball grid array (BGA) groups (i.e., size, ball count and pitch) was baselined using IC. We processed two replicates for each group because we had a limited number of parts to work with. The BGAs were then sent to be re-balled using a standard robotic reballing process. The ionic cleanliness of each group was then re-evaluated using the ROSE test as defined in the GEIA-STD-0006 and again with IC. The solvent volumes used for each test were 5ml for the IC test and 98ml for the ROSE test.
The different ions listed in Figure 1 are from the IC test. As we have indicated, IC has considerably greater selectivity than does ROSE and can identify specific ion species from a sample extract. At the bottom of the table is a red circle around the ROSE and IC results. The ROSE result is expressed as μg of NaCl equivalents per square centimeter. It is important to understand that this is neither a measurement of sodium nor chloride, but an expression of the result compared to a standardized solution of a NaCl salt, which is used to standardize the instrument. The IC results are given as micrograms of ion per square centimeter. The IC results are direct measurements made back to certified standards of specific ion species. Each ion species is calibrated separately.
To read the full article, which appeared in the August 2018 issue of SMT007 Magazine, click here.
Suggested Items
Nanotechnology Market to Surpass $53.51 Billion by 2031
04/25/2024 | PRNewswireSkyQuest projects that the nanotechnology market will attain a value of USD 53.51 billion by 2031, with a CAGR of 36.4% over the forecast period (2024-2031).
Vicor Power Orders Hentec Industries/RPS Automation Pulsar Solderability Testing System
04/24/2024 | Hentec Industries/RPS AutomationHentec Industries/RPS Automation, a leading manufacturer of selective soldering, lead tinning and solderability test equipment, is pleased to announce that Vicor Power has finalized the purchase of a Pulsar solderability testing system.
D Coupon Testing and Data Insights With GreenSource Fabrication
04/17/2024 | Marcy LaRont, PCB007 MagazineMarcy LaRont spoke with Steve Karas of GreenSource Fabrication at the SMTA UHDI conference in March. He presented a case study that GreenSource undertook with a customer on critical via reliability with advanced materials and used the experience to highlight the importance and effectiveness of D coupon testing. He also discussed GreenSource’s approach to data aggregation and a new system they developed to use collected data effectively.
Three Industry Leaders Receive IPC President’s Award
04/17/2024 | IPCIn recognition of their leadership and significant contributions of time and talent to IPC and the electronics industry, three IPC volunteers were presented with the IPC President’s Award at IPC APEX EXPO in Anaheim, Calif., on April 9, 2024.
Yamaha to Showcase Latest-generation Assembly Equipment and Software Tools at SMTconnect
04/16/2024 | Yamaha Robotics SMT SectionYamaha Robotics SMT Section will team with its distributor ANS Elektronik to showcase innovations for high-speed surface mount assembly at SMTconnect 2024.