-
- News
- Books
Featured Books
- smt007 Magazine
Latest Issues
Current IssueBox Build
One trend is to add box build and final assembly to your product offering. In this issue, we explore the opportunities and risks of adding system assembly to your service portfolio.
IPC APEX EXPO 2024 Pre-show
This month’s issue devotes its pages to a comprehensive preview of the IPC APEX EXPO 2024 event. Whether your role is technical or business, if you're new-to-the-industry or seasoned veteran, you'll find value throughout this program.
Boost Your Sales
Every part of your business can be evaluated as a process, including your sales funnel. Optimizing your selling process requires a coordinated effort between marketing and sales. In this issue, industry experts in marketing and sales offer their best advice on how to boost your sales efforts.
- Articles
- Columns
Search Console
- Links
- Events
||| MENU - smt007 Magazine
Estimated reading time: 2 minutes
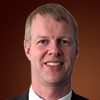
What is Your Real Output?
How should you define your output? Highest area productivity, lab speed, actual speed, optimum speed, IPC speed, or maximum speed? And is it speed or throughput we should be looking at? Neither is clearly defined, and we all have our rules of thumb (e.g., actual speed is 60% of IPC speed, which is 60% of maximum speed).
Currently, there is only one standard representing a fair comparison between pick-and place equipment: IPC-9850. It measures equipment speed (providing that components are placed within the specified accuracy of the equipment itself). IPC established IPC-9850 in 2002, defining the measurement procedures for specifying, evaluating and verifying surface mount placement equipment. With machine manufacturers producing a wide range of accuracies and outputs, it details how measurements must be made consistently, and is therefore the only real way to compare them. It has become a basic industry reference, but unfortunately doesn’t tell the whole story. Several pick-and-place machine manufacturers, for example, currently claim the industry’s fastest placement speeds on the basis of the IPC reference speed.
One key difference lies between the IPC-9850 speed and the actual speed you will reach in a particular application. And that is where IPC-9850 falls short.
For this reason, IPC published an updated version in January 2012: IPC-9850A. Since the release of this update, it has been adopted by…practically nobody. Admittedly, the new standard is far from perfect, as applications are usually still more complex than even it allows for. It is a step closer to the truth, though. Why have so few adopted it? Why do most manufacturers avoid publishing the results? It seems that this minor change in specification degrades output results so drastically that it is commercially too sensitive.
IPC-9850 and IPC-9850A: The Differences
IPC-9850 speeds are measured by placing a simple matrix of components (for example 80 SOIC-16s or 400 identical 0603 capacitors) on a 200 x 200 mm substrate. However, the standard says nothing about the electrical value of these 400 capacitors, for example. That allows sequential placement machines to use gang pick (simultaneous pick by multiple placement heads) using an optimized placement path. Gang pick, however, artificially inflates the performance figure since it can virtually never be used in an actual customer application. You just don’t get many circuits incorporating hundreds of identical 27-nF capacitors on a board in a small matrix in a 200 x 200 mm area.
Read the full column here.
Editor's Note: This column originally appeared in the March 2014 issue of SMT Magazine.
More Columns from SMT Trends & Technologies
SMT Trends and Technologies: What is Your Real Output?SMT Trends & Technologies: Goodbye to Trial and Error?
SMT Trends and Technologies: Pick and Paste
SMT Trends and Technologies: Doing More Than One Thing at a Time
SMT Trends & Technologies: Clash of Clans - The New Expansion of PCB Assembly Equipment
Goodbye to Trial and Error?